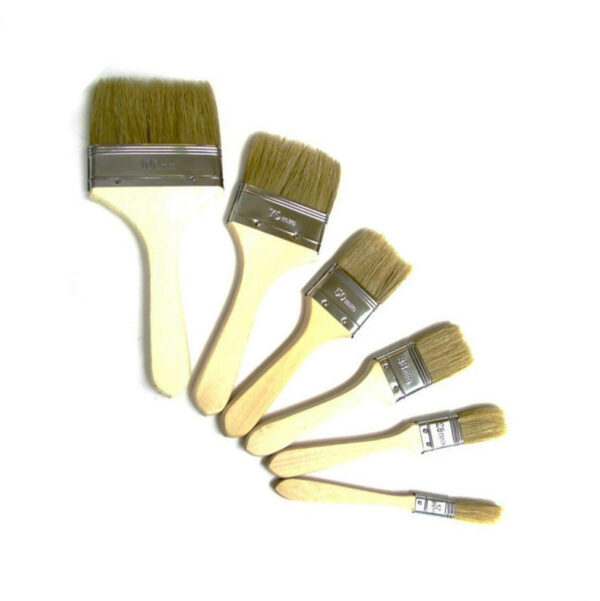
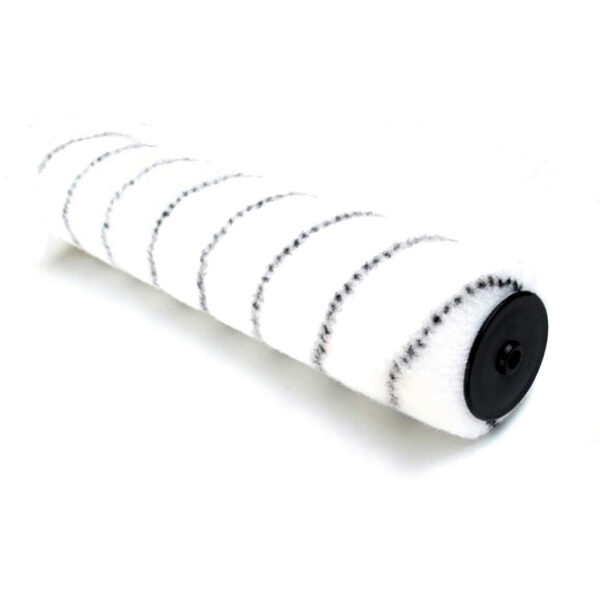
Anticorrosive High Build Phosphate Quick Dry Primer
£34.50 – £72.50 ex VAT
Anticorrosive High Build Phosphate Quick Dry Primer is a single pack priming solution suitable for most metal substrates. This metal paint is also suitable for pre-treated aluminium and galvanised steel. High Build Phosphate Quick Dry Primer gives excellent protection against corrosion. Excellent build levels and can be re-coated in most types of finish.
– Coverage: 5 m² per litre
– Touch Drying Time: 30 mins – 1 hr
– Recoat: 12 hrs
– Hard Drying Time: 24 hrs
[block id=”47497″]
BULK ORDERS? CALL 01782 550733 FOR DISCOUNTS!
Available Metal Primer Colours
*The colours of metal paints shown in this chart are approximate and may vary.
Technical Details
[row]
[col span__sm=”12″]
[message_box text_color=”light” padding=”10″]
[row_inner v_align=”middle” h_align=”center”]
[col_inner span=”8″ span__sm=”12″]
Anticorrosive High Build Phosphate Quick Dry Primer Reviews
[/col_inner]
[col_inner span=”4″ span__sm=”12″ align=”right”]
[button text=”READ REVIEWS / LEAVE FEEDBACK” color=”white” style=”outline” expand=”0″ link=”https://regalmetalpaint.co.uk/high-build-phosphate-quick-dry-primer-reviews/”]
[/col_inner]
[/row_inner]
[/message_box]
[/col]
[/row]
[ux_pages parent=”4794″ columns=”6″ image_height=”50%” text_align=”center” text_size=”small”]
Weight | N/A |
---|---|
Select Colour |
Red Oxide ,Light Grey ,Black ,White |
Select Size |
5 Litres ,20 Litres |
FAQs
Deprecated: html_entity_decode(): Passing null to parameter #1 ($string) of type string is deprecated in /www/regalwoodmart_298/public/wp-content/plugins/ultimate-faqs/includes/template-functions.php on line 354
FAQ High Build Phosphate Quick Dry Primer
Over the years there has been a lot of misinformation provided concerning red oxide, primarily due to its widespread use in red oxide primers where its principal application is to camouflage rust creeping through from the steel underneath. Red oxide is actually the common name for iron III oxide (Fe203) which in colour and chemically is very similar to the hydrated iron oxide (rust) which hides any early signs of rust. Red iron oxide when purified and sold as a pigment for use in paint and ceramics has the advantage of being stable having already oxidised and so resistant to further oxidation and heat changes at most temperature found in common applications. It is also hard and very resistant to mechanical damage. All of these characteristics have led to its widespread use in primer paints or direct to metal paints for iron and steel for many decades. However, unless combined with an active pigment, usually a phosphate to protect the steel there is little actual protection provided by the red iron oxide other than as barrier and here it is often confused with a more effective form of barrier coating based in micaceous iron oxide which is another form entirely and uses its lamellar plate like structure to provide some physical barrier to the penetration of water and oxygen, both of these are needed for corrosion to take place.
Corrosion is an electrochemical process, very much like a battery in which the iron in steel is oxidised by losing electrons to become positively charged iron ions:
Fe » Fe2+ + 2e-
The electrons produced by this reaction combine with hydrogen ions in the water as well as with dissolved oxygen to produce water:
The formation of rust requires iron, water and oxygen. Although it’s a complex process, the chemical equation is simply:
4Fe + 3O2 + 6H2O → 4Fe(OH)3.
The First Step: Oxidation of Solid Iron
It’s common knowledge that rust occurs when you leave water on a metal implement or you leave it exposed to moist air. That’s because the first step in the rusting process involves the dissolution of solid iron into solution. The formula for this is:
Fe(s) → Fe2+(aq) + 2e-
The electrons produced by this reaction combine with hydrogen ions in the water as well as with dissolved oxygen to produce water:
4e- + 4H+(aq) + O2(aq) → 2H2O(l)
The consumption of hydrogen ions that occurs as iron dissolves leaves a preponderance of hydroxide (OH-) ions in the water. The iron(II) ions react with them to form green rust:
Fe2+(aq) + 2OH–(aq) → Fe(OH)2(s)
BUT that isn’t the end of the story. The iron(II) ions also combine with hydrogen and oxygen in the water to produce iron(III) ions:
4Fe2+(aq) + 4H+(aq) + O2(aq) → 4Fe3+(aq) + 2H2O(l)
These iron ions are the source of the reddish deposit that gradually eats holes in all corroding steel and iron from car bodywork to metal roofing to farm ironwork. They combine with the extra hydroxide ions to form iron(III) hydroxide:
Fe3+(aq) + 3OH–(aq) → Fe(OH)3
This compound dehydrates to become Fe2O3.H2O, which is the chemical formula for rust. Note how similar it is t the chemical formula for Red iron oxide pigment Fe2O3 and this is why red iron oxide paints help to camouflage but do not prevent corrosion when used as red iron oxide primers or paints – for that you need a pigment that actively prevents corrosion such as Nanoguard ACP
Anti corrosive pigments? What are they? Here we try to give a simple explanation.
Over the years, many products have been used (to a greater or lesser degree of success) in the prevention of corrosion, often together with red oxide to produce a red oxide metal primer.
The purpose of primer paints is to act as preparation, forming part of the protective coating for the underlying metal and inhibiting rust formation.
In the past, toxic pigments such as red lead, and carcinogenic pigments such as chromates, have been used. However, due to health concerns they were replaced largely by zinc phosphate. In turn, this old technology was found to be very bad for the environment leading to its replacement by zinc-free systems, replacing the harmful heavy metal zinc with the friendly metal calcium. Since calcium phosphates are widely found in our bodies there are no harmful effects on either human health or the environment from this technology and so modern formulations tend to be zinc-free.
Early versions of zinc-free anti-corrosives first appeared in the late 1980’s when BP became concerned about the leaching of heavy metals and things like zinc-based paints into the sea from their oil rigs. This earlier technology, based on calcium ion exchanged silica, has gradually been superseded by a variety of calcium-phosphate based products such as Nanoguard ACP DCP and Nanoguard ACP2 (used to replace carcinogenic chromates).
Formulation of metal protection products, including direct-to-metal products such as the traditional hammer-finish paints and epoxy coatings, now widely use calcium-phosphate to protect metalwork. With a pedigree developed for the harsh environment of the North Sea oil fields these zinc-free phosphates continue to provide longevity to steel structures around the world without damaging the environment or our health.
Here at Industrial Protective Paints Ltd, all of our products that require anticorrosive properties, for example Regal Anticorrosive Primers and Regal Skip and Container Paint, are manufactured using calcium-phosphate technology.
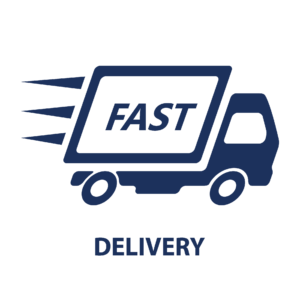
WE AIM TO DISPATCH ORDERS RECEIVED PRE-NOON ON THE SAME DAY (STOCK DEPENDENT)
ALL ORDERS SENT ON A NEXT WORKING-DAY SERVICE
FREE DELIVERY ON ALL ORDERS OVER £300*
*£300 NET. Excludes surcharge areas - delivery surcharge will still apply.